- 1-800-4-REBUILD
- admin@precisionservicemtr.com
- 121 W. Fullerton Avenue Addison, IL 60101
REBUILD
The term “rebuild” refers to a complete overhaul of a machine to its original mechanical specifications. The mechanical components of the machine are cleaned, inspected, and rebuilt using either new or re-machined parts.
- See More Below!
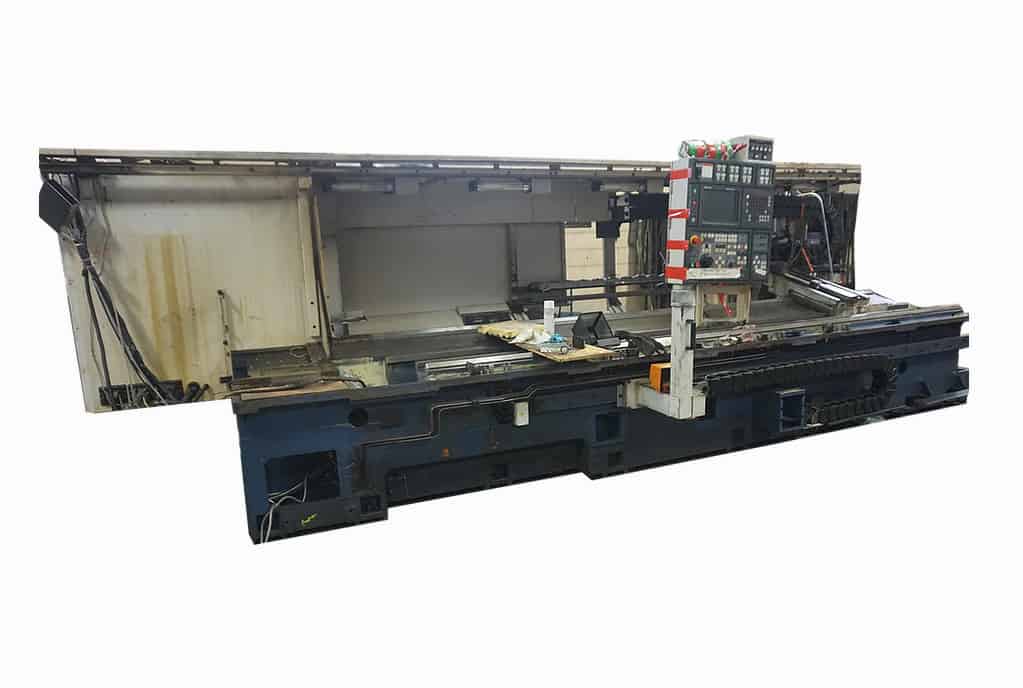
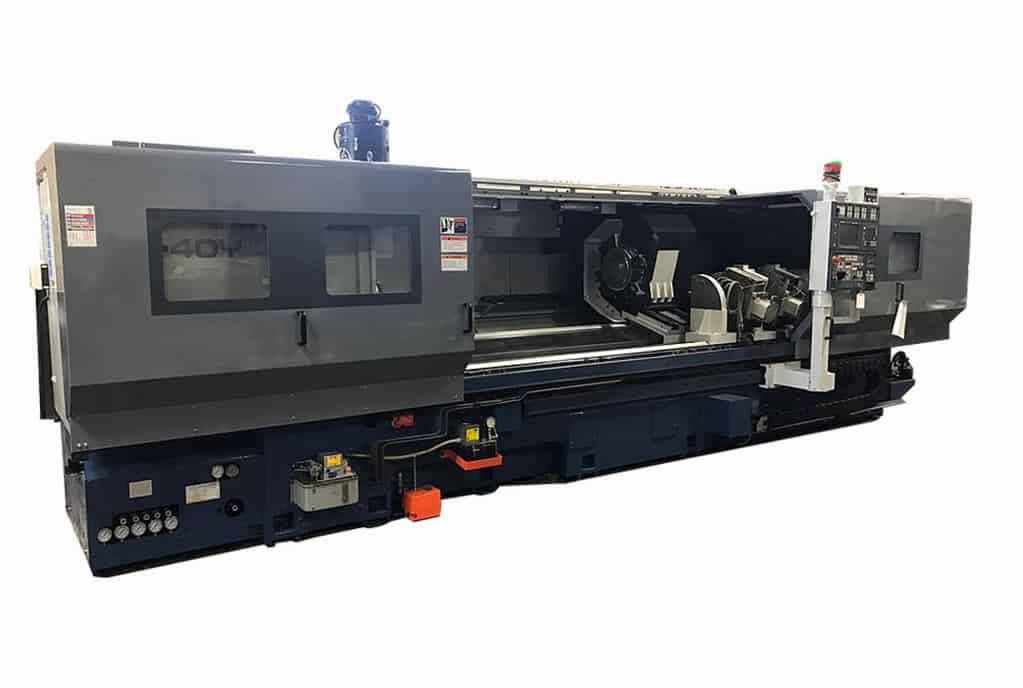
RESTORING YOUR MACHINE TO LIKE-NEW CONDITION
Precision Service technicians are experts in restoring the condition of your machine to its original operating condition. We understand that your machine is an important aspect of your everyday operations. This pushes us to work in a timely manner to repair or rebuild your machine to get it back in action as soon as possible, saving you time and money.
Getting your machine back to full production is simple! Just call Precision Service MTR where honesty is our policy. We will tell you the truth about what needs to be done and provide you with an honest quote. As a family owned and operated business, we are a Service Partner you can trust!
Featured Rebuild Projects
Nakamura Tome TW-10
Mori Seiki TL-40Y
Kellenberger Grinder
Leblond Lathe
Mazak Slant Bed
Oster 716
Landis Threader
Fadal Mill
Mazak Slant Bed
Mazak M5N
"T" Lathe
Mazak Powermaster
Gallmeyer & Livingston Grinder
Mori Seiki ZL-45M
Spindle Rebuild
NAKAMURA TOME TW-10
- Disassemble complete machine
Rebuild main and sub spindle
Install new linear guides
Scrape spots of bed due to rust
Precision aligned linear guides square to each other
Align turrets to spindle, center lines to new ballscrews
Scrape and align new ballscrew brackets on all axis due to rust
- New lubrication system
- Install new spindle drive belts
Rebuild both turrets
Replace hydraulic pump due to leaks
Replace hydraulic and coolant hoses
Replace seal tight
Clean and inspect all drives and boards
Paint and reassemble
MORI SEIKI TL-40Y
Disassemble complete machine
Grind bed ways, upper and lower
Scrape and align headstock base to bed ways
Supply and install turcite to bottom of saddle ways, keeping saddle square to spindle
Way grind top of “X” axis ways
Scrape, flake and master bottom ways of cross slide to saddle
Way grind “Y” axis ways
Precision align “Y” axis to original factory tolerance
Scrape and flake “X”, “Y” and “Z” axis gibs. Upon completion, gibs to have full adjustment
Scrape and master tailstock to bed way keeping parallel to spindle and spindle center line
Align turret to spindle center line
Scrape and align ball screw brackets for flatness (“X”, “Y”, and “Z” axis)
Precision align “X”,”Y”, and “Z” axis ball screws
Replace all lubrication meters and lines as required to assure proper lubrication to all required areas
Install new way wipers
Reassemble and test all machine functions
Kellenberger Grinder
Disassemble and clean machine
Hand scrape and flake all way surfaces true to each other
Rebuild hydraulic pump valves and replace hoses
Rebuild and replace mechanical locks and stops
- Clean electrical system
Replace broken wire and sealtite
New lubrication system
Replace all line and meters
Paint machine to customer code and reassemble
LEBLOND LATHE
Dismantled machine, cleaned, prepped for rebuild
Way ground bed ways to “0” with a clean like new finish
Scraped and aligned saddle to bed using turcite to keep centerline true replacing all metal that was machined and scraped
Scraped and aligned crosslide to top of saddle
Scraped and aligned compound slide
Ground and refit all binders
Scraped and fitted all gibs ensuring full adjustment
New way wipers to keep machine ways debris free
Cleaned and flushed lubrication making sure all lube lines were replaced as needed and new meters installed for proper oil flow to entire machine
New lead screws, thrust bearings, and seals installed on all axis’s
Sanded and painted machine
Reassembled machine back to spec
Powered up and test cut parts giving this Leblond lathe a better than new quality
MAZAK SLANT BED
Dismantled machine tool
Cleaned and visually inspected all units
All components readied for customer’s inspections
Machine, scraped, ground and fit all quoted ways surfaces to full bearing, assuring longer life of all necessary components
Way ground bed ways
Scraped and aligned headstock base to bed, keeping parallel to ways
Way ground “X” axis ways
Scraped and aligned “X” axis slide to “Z” axis bed ways, keeping parallel and square to bed ways
Scraped and flaked all gibs in “Z” axis, leaving maximum adjustment
Scraped ATC slide to “X” axis slide, keeping parallel and square to spindle center line
Scraped and flaked all gibs in “X” axis, leaving maximum adjustment
Scraped, flaked and mastered tail stock to bed way, maintaining spindle center line
Rebuilt “X” and “Z” axis ball screw and nuts
Supplied and installed thrust bearings in “X” and “Z” axis
Realigned “X” and “Z” axis ball screw parallel to axis ways
Cleaned and checked hydraulic system
Replaced damaged or defective hydraulic lines
Surveyed hydraulic pump and motor
Cleaned, inspected, repaired lubrication system in areas of repair, assuring proper oil flow to all required areas
Replaced damaged or defective lube lines and installed new flow units
Supplied and installed new spindle belts
Supplied and installed new way wipers
Replaced seals
Surveyed pocket and pin
Precision aligned to center line of spindle
Megered all axis motor
Assembled and test machine
Set all prox switches, roller switches, roller switches back last comp. tool eye
Checked “droop” and “gain” of all axis
Machine tool was demonstrated for personnel at Precision Service facility
All alignment met or exceeded those of the O.E.M.
OSTER 716
Dismantled Machine tool
Cleaned and visually inspected all units
After cleaning all components and structural castings were carefully inspected for overall condition
Machine, scraped, ground and fit all quoted way surfaces to full bearing, assuring longer life of all necessary components
Ground bed ways, upper and lower
Ground clamping areas of bed
Supplied and installed turcite to bottom of saddle ways
Scraped saddle to bed, keeping saddle square to spindle
Scraped and flaked gibs
Aligned saddle to spindle center line
Cleaned and inspected hydraulic systems
Replaced filters
Replaced all lubrication meters and lines as required to assure proper lubrication to all required areas
Installed new way wipers
Inspected headstock gears
Replaced headstock bearings
Reassembled machine completed and tested all machine functions
LANDIS THREADER
Dismantled Machine tool
Cleaned and visually inspected all units
After cleaning all components and structural castings
were carefully inspected for overall conditionGround bed ways, upper and lower
Ground clamping areas of bed
Supplied and installed turcite to bottom of saddle ways
Scraped saddle to bed, keeping saddle square to spindle
- Scraped and flaked gibs
Aligned saddle to spindle center line
Cleaned and inspected hydraulic systems
Replaced filters
Replaced all lubrication meters and lines as required to assure proper lubrication to all required areas
Installed new way wipers
Reassembled machine completed and tested all machine functions
FADAL MILL
Dismantled machine tool units
Cleaned and inspected all quoted components
All components readied for customers inspection
Machine, scraped, flaked, and fit all quoted way surfaces to full bearing; assuring manufacturer’s specifications and alignments
Removed saddle and table from bed ways
Removed table from saddle
Way ground top of saddle ways, master and gib ways, and binder
Removed old turcite from bottom of table
Supplied and installed new material to bottom of table
Scraped master table and saddle, made table 4 corners 0 to top of table
Supplied and installed material to table gibs and binders
Scraped and fitted table gibs and binders to saddle
Supplied and installed material to bottom of saddle
Scraped master saddle to bed to keep square and parallel to bed ways
Supplied and installed material to saddle gibs and binders
- Supplied and installed material to saddle gibs and binders
Scraped and fitted saddle gibs and binders to bed
Aligned ball screw for table and saddle
The head was removed from column
The ways were cleaned and polished to best as condition
New turcite was installed on head
The head was scraped and precision aligned to column
The binders and gibs were refit
Turcite was installed as required
Gibs were scraped and fit, upon completion, gibs brought to full adjustment
Precision Service sent all ball screws out for inspection
Installed thrust bearings in all axis
Cleaned, inspected, repaired lubrication system in areas of repair; assuring proper oil flow to all required areas
Assembled and test ran machine
Set all proximity switches
MAZAK SLANT BED
- Dismantled machine tool
Cleaned and visually inspected all units
Way ground bed ways
Scraped and aligned headstock base to bed, keeping parallel to master way
Scraped and aligned saddle to bed using turcite to keep machine centerline true
Scraped and flaked all gibs, ensuring max adjustment
Scraped ATC slide to X axis slide, keeping slide parallel and square to spindle center line
Scraped and flaked tail stock to master bed way, maintaining spindle center line
- Installed rebuilt ballscrews, thrust bearings, and seals
Cleaned and flushed hydraulic system
Replaced all corroded and damaged hydraulic lines
Surveyed hydraulic pump and motor
Cleaned and inspected lubrication system for any flaws or damaged areas that need repair, assuring proper oil flow to all required areas
Replaced damaged and defective lube lines, installed all new oil meters
Supplied and installed new spindle belts
Supplied and installed new way wipers
MAZAK M5N
Dismantled Machine tool
After cleaning all components and structural castings were carefully inspected for over-all condition
Machine, scraped, ground and fitted all quoted way surfaces to full bearing, assuring longer life of all necessary components
Surveyed Headstock spindle found no lift check out good
Headstock gears, pinions, input shafts and pulleys were surveyed for excessive wear, cracks and other defects
Found input shaft keys where worn replace with new with new bearings
Ground bed ways and clamping areas
Scraped bottom of headstock base to the bed ways
Supplied and installed turcite to bottom of saddle ways
Hand scraped saddle to bed, keept saddle square to spindle
Way ground top of “X” axis ways removing worn area
Scraped, flake bottom ways of cross slide to saddle
Scraped and flake “X” and “Z” axis gibs to have full adjustment
Tailstock quill was refitted for proper fit to housing
Replaced tailstock seals and bearings
Installed turcite to tailstock base
Scraped tailstock to bed way keeping parallel to spindle and spindle center line
Installed all new seals, packings and bearings in both turrets
Aligned front and rear turret to spindle center line
Sent out “X” and “Z” axis ballscrews to be reconditioned
Installed thrust bearings in “X” and “Z” axis
Scraped and aligned ball screw brackets for flatness (“X” and “Z” axis)
Precision aligned “X” and “Z” axis ball screws
Cleaned hydraulic systems replace filters and all sight glasses
Replaced all lubrication meters and lines as required to assure proper lubrication to all required areas
Installed all new way wipers
Painted machine standard Mazak color code
"T" LATHE
- Dismantled Machine tool
Surveyed headstock spindle and bearings for axial and radial clearance
New bearings where needed due run out and lift
Headstock gears, pinions, and pulleys will be surveyed. No need to be replaced but found input shaft key way where worn replaced with new
Hand scraped and aligned bed square and parallel to spindle
Scraped saddle to bed, keeping saddle square to spindle
Way ground top, leading edge of “X” axis ways
Scraped, flaked and mastered bottom ways of cross slide to saddle
Machine scraped and aligned “Z” axis compound ways
Precision aligned compound square turret to top of compound slide
Scraped and flaked “X” and “Z” axis gibs to have full adjustment
Remanufactured “ X” and “Z” axis ballscrews
Installed new thrust bearings on “X” and “Z” axis ballscrews
Scraped and aligned ball screw brackets for flatness (“X” and “Z” axis)
Precision aligned “X” and “Z” axis ball screws
Cleaned and inspected hydraulic systems
Replaced all hydraulic hoses, filters and sight glasses
Removed and replaced all lubrication meters and lines, retrofit with Lube LHL x 100 grease system and Generation 3 LHLPX1 retrofit panel
Supplied and installed all new way wipers
Installed new spindle drive belts
Painted machine to customers color code
MAZAK POWERMASTER
Dismantled Machine tool
After cleaning all components and structural castings were carefully inspected for over-all condition
Machine, scraped, ground and fit all quoted way surfaces to full bearing, assuring longer life of all necessary components
Surveyed Headstock spindle found no lift check out good
Headstock gears, pinions, input shafts and pulleys were surveyed for excessive wear, cracks and other defects
Found input shaft keys were worn, replaced with new with new bearings
Ground bed ways and clamping areas
Scraped bottom of headstock base to the bed ways
Supplied and installed turcite to bottom of saddle ways
Hand scraped saddle to bed, keeping saddle square to spindle
Way ground top of “X” axis ways removing worn area
Scraped, flake bottom ways of cross slide to saddle
Scraped and flaked “X” and “Z” axis gibs to have full adjustment
Tailstock quill was refitted for proper fit to housing
Replaced tailstock seals and bearings
Installed turcite to tailstock base
Scraped tailstock to bed way keeping parallel to spindle and spindle center line
Installed all new seals, packings and bearings in both turrets
Aligned front and rear turret to spindle center line
Sent out “X” and “Z” axis ballscrews to be reconditioned
Installed thrust bearings in “X” and “Z” axis
Scraped and aligned ball screw brackets for flatness (“X” and “Z” axis)
Precision aligned “X” and “Z” axis ball screws
Cleaned hydraulic systems, replaced filters and all sight glasses
Replaced all lubrication meters and lines as required to assure proper lubrication to all required areas
Installed all new way wipers
Painted machine standard Mazak color code
GALLMEYER & LIVINGSTON GRINDER
Dismantled machine tool
Cleaned and visually inspected all parts
All component readied for customer’s inspection
Machine, scraped, flaked and fitted all quoted way surfaces to full bearing, assuring longer life of all necessary components
Lathe tested spindle for concentricity and alignment
Repaired spindle bearing lands
Supplied and installed spindle bearings our datum point
Scraped and flaked column ways flat and parallel
Scaped, flaked and master spindle assembled to column ways, indicating 4 points “0”
Scraped and flaked bed ways flat and parallel to spindle
- Scraped, flaked and mastered bottom saddle ways to bed ways
Scraped and flaked table flat and parallel to our master granite plate
Scraped, flaked and mastered table ways to top of saddle ways
Repaired Gibs
Scraped, flaked and mastered all gibs and clamps
Cleaned, inspected and repaired lubrication system in areas of repair, assuring proper oil flow to all required areas
Supplied and installed all screws and nuts
Rebuilt table cylinders
Hydraulic system was cleaned and flushed
All hydraulic lines damaged, or fittings were replaced with new
Template is not defined.
SPINDLE REBUILD
Removed wheel head assembly
Removed spindle from wheel head and inspected
Cleaned headstock
Sent spindle out for ceramic coating on bearing surface
Ground spindle
Supplied and installed new spindle bearing, front and rear
Scraped and fit spindle to new spindle bearings
Cleaned and checked spindle lube system
Transported wheel head assembly back to customer
Reassembled wheel head on machine
Adjusted gibs and related parts
Inspected lube to assure proper lube to related parts
Test ran spindle set pressure switches when complete
Common machine tool repair/rebuild operations Precision Service handles include
Replacement of parts
Spindle Repair and Rebuild
Ball Screw Repair and Replacement
Machine/Grind/Scraping
Replacement of Linear Way
Machine, Grind, Hand scrape, and fit all moving machine surfaces
Ensure full bearing and accurate alignment
Apply Turcite, Moglice, or Phenolic
Replace Lubrication for longevity of the ways surfaces
Final testing and inspection
Test run to new machine standards
INTERESTED? REQUEST A QUOTE TODAY ➞